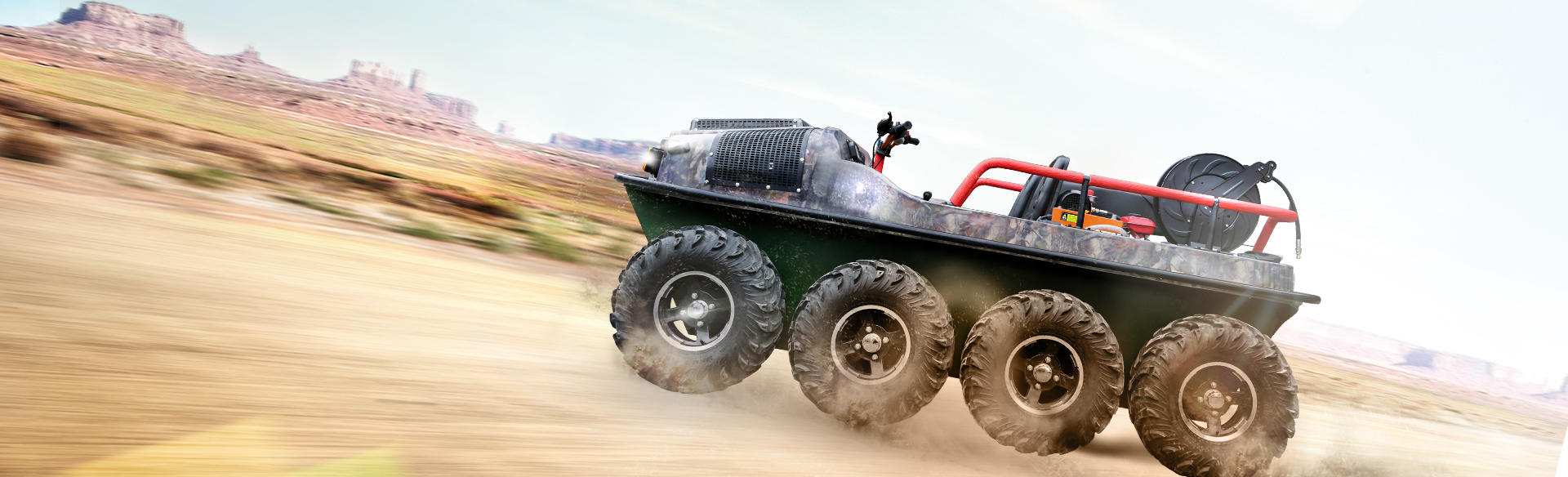
How to extend the service life of rubber tracks
Clean the landing gear frequently. Clean the tracks as frequently as possible to prevent the accumulation of dirt and debris in the chassis components. Packing prevents proper engagement between mating parts (such as sprocket teeth and track links). This leads to increased load and wear rate of chassis components. If you are working uphill, transfer the weight of the machine to the rear. This increases the load on the rear rollers and increases the wear on the front drive side of the sprocket teeth and connecting rods. When reversing downhill, the load on the landing gear is lighter. When working downhill, transfer the weight to the front of the machine. Additional loads will be applied to the front rollers, idler tread and track links.
When you reverse uphill, the connecting rod will rotate against the reverse side of the sprocket. This helps to evenly wear the links on steel and rubber tracks. Working on a slope or side slope will transfer weight to the downhill side of the machine and cause additional wear on the roller flanges, the sides of the crawler links and the ends of the crawler teeth. Balance the wear between the sides of the chassis by changing the working direction on the slope. It is important to try to reduce the slippage and rotation of steel and rubber tracks.
Slippage and skidding will accelerate the wear or tread depth of the track teeth of the crawler track and limit the production efficiency. Severe contact between sprocket teeth, track links, rollers and idler tire surfaces will accelerate wear. Constantly turning to one side will reduce the life of the rubber or steel track. If possible, plan your work to balance the rounds. Limit unproductive high-speed driving, because high-speed operation will accelerate the wear of all chassis components. Track wear is proportional to speed. Speed ??will increase pressure. The distance traveled by the crawler machine determines the wear. Try to limit reverse operation. Reverse operation will accelerate the wear on the reverse drive side of the track links and sprocket teeth. Plan your site work carefully to make the trip productive.